Our Production
Made in Sweden
A black door takes you into the building. Welcome to the LINTEX factory, to the staff, the crafts and the machines. This is where the products are manufactured. Quality is at the core of the brand and it is born when carefully designed writing boards, office screens and noticeboards are built in the controlled setting which is a modern factory. LINTEX products don’t turn up from anonymous manufacturers on the other side of the planet. They are created here in the LINTEX factory in the small town of Nybro in southern Sweden. LINTEX moved in 2009 into a disused factory that had previously made kitchen-cabinet fronts, building up its production and extending the premises . In room after room materials are stored in racks and on shelves with scanners keeping track of every last detail. Everywhere you find solutions to problems. LINTEX writing boards are manufactured using handcraft in combination with clever machines and the best form of lo-tech linked to computers. The company’s self-developed, complex apparatus is essential in achieving rational production. A stage that formerly took 45 minutes by hand can now be done in 10 minutes. Time-saving is essential if production is to remain in Sweden.
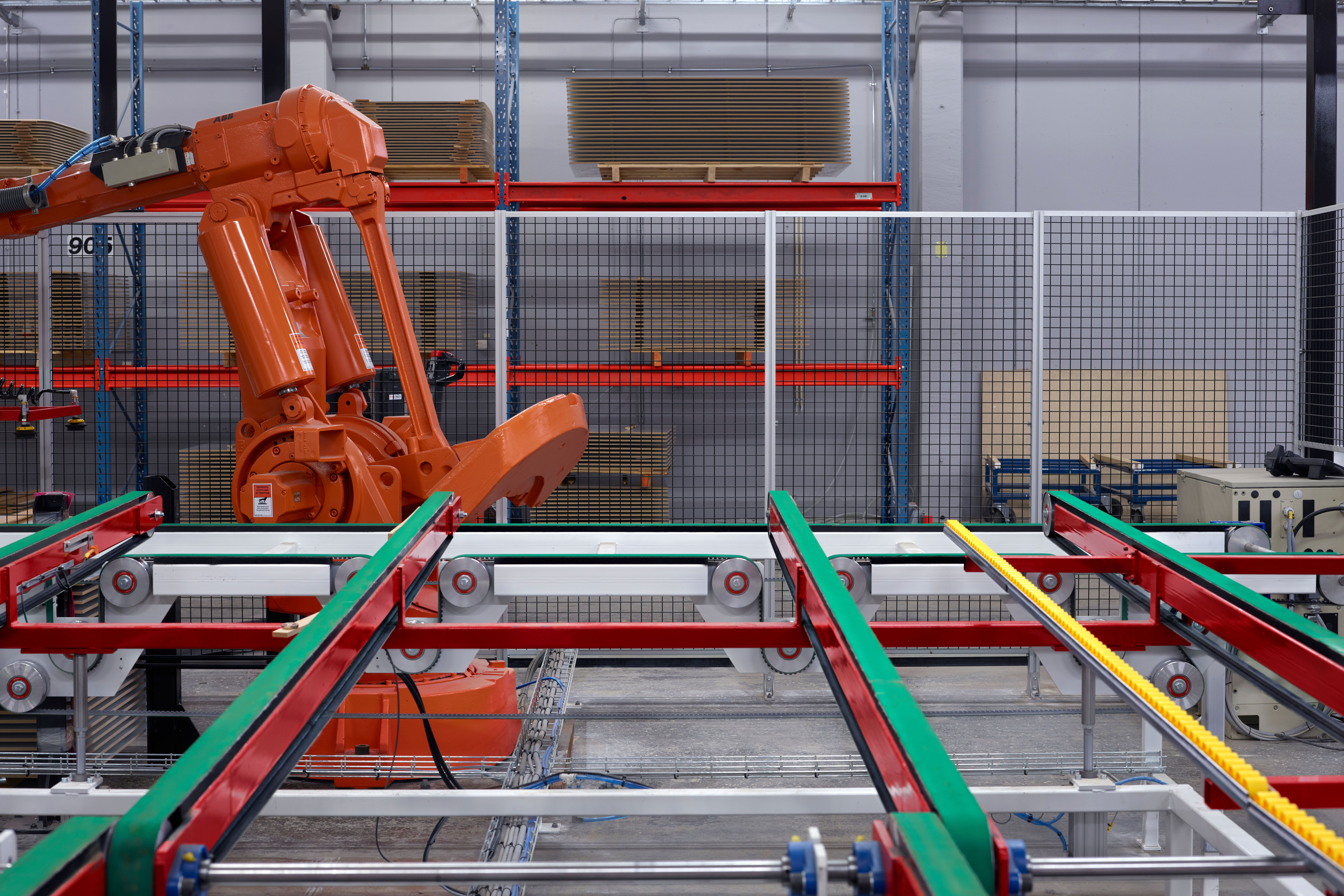
Rolls of textile are stored in a room with numbered slots all over the walls. This is to prevent the staff from collecting the fabric from a large pile, involving heavy lifts. Ergonomics is decisive. Now the fabric rolls are lifted elegantly from their slots with a special trolley. They are then placed on the cutting table and cut by a pre-programmed machine. The cut fabrics move on to the upholsterers where wooden frames – made by a local carpenter – are dressed. The skill is evident in the rapid hand movements around the frame. Large orange robots lift boards, sort them, and position them with jerky movements. Boards are cut using razor-sharp CNC programming. Ten boards already cut and another ten before the coffee break at 2 pm sharp. A seemingly indestructible machine glues the board elements together with enamelled steel. A carpenter works on wooden frames in massive oak. Mitre joints are a sensitive issue. They need to meet up with such precision that only the fingertips can feel the joins. It is here that the tiny details in wood or metal reveal LINTEX’ level of quality. No room for short cuts.
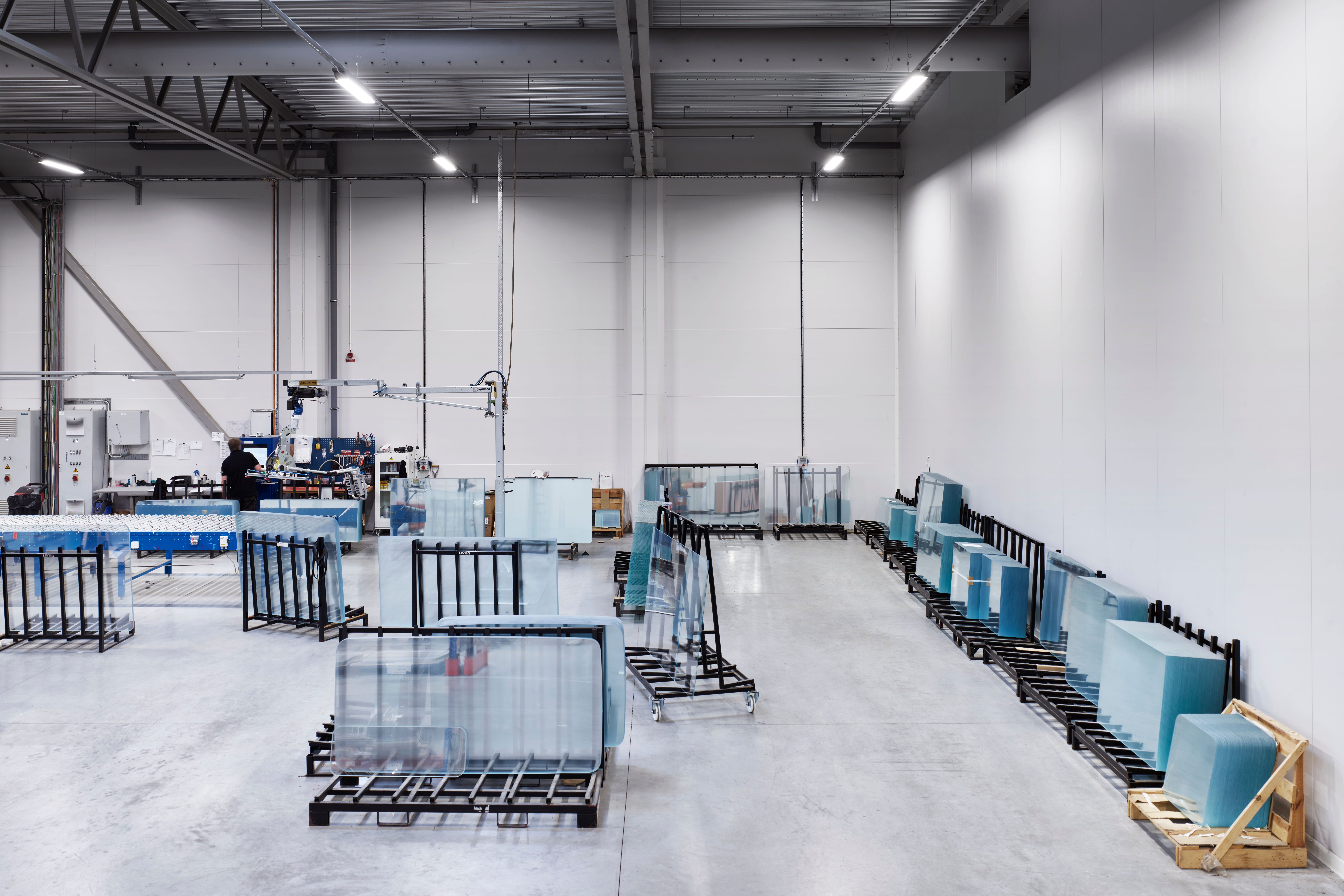
Step by step, raw materials and the various product parts are joined together to produce the LINTEX products. The processes reveal the extreme care about materials, environmental issues and logistics. All of the staff in the factory share a special LINTEX spirit of caring and pride. Some are new to the firm while others have worked there for decades. Many of them come from woodworking factories, or from glassworks in the district. The mood is positive and there is plenty of ribbing and discussion. Respect for craft skills is omnipresent. Every part of a product is worked on by many hands. At every stage of production there are quality controls to ensure that no faults or sloppy fits slip through.
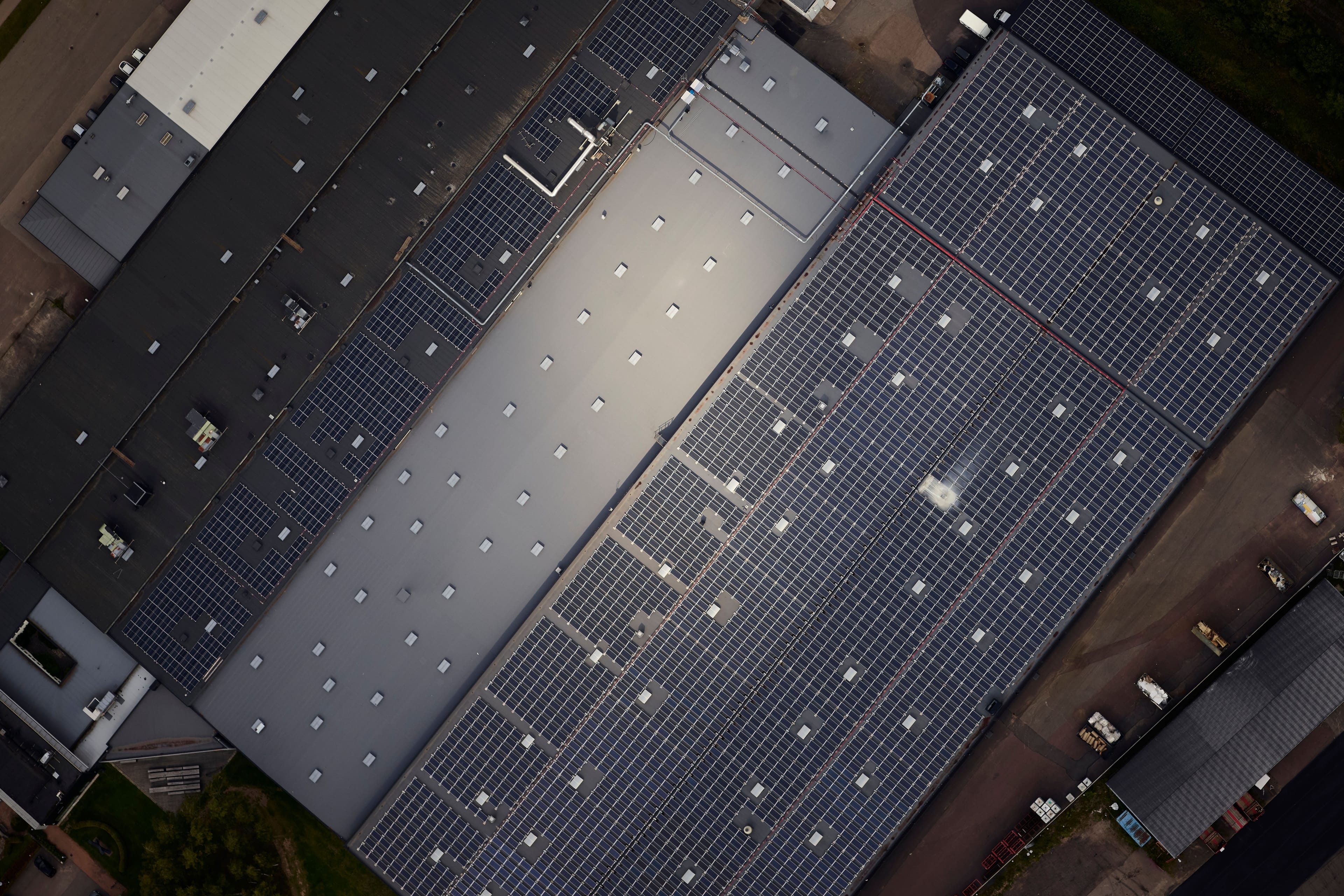
The work of the factory is determined at detail level by an advanced computer system keeping track of all inputs, outputs, finished details on a particular morning, tempo, time, deliveries and so on. LINTEX prides itself on its rapid deliveries, frequently within two weeks of ordering and sometimes within two days if it is a standard product from storage. Lorries back into the factory, LINTEX products are loaded inside and the lorries depart for Berlin, Basel, Lausanne, Italy, the UK, Finland. The entire world is waiting beyond the loading bays of the Nybro factory.
Text: Petter Eklund
Photos: Brendan Austin